SynerFlux
Parce que la rationalisation des flux est la base du Lean Manufacturing, tout projet de reengineering doit commencer par la simplification des flux physiques et d’informations.
En Application des MÉTHODOLOGIES bien connues, 2 exemples illustrant l’éventail de nos INTERVENTIONS
De la petite mission de 10 jours dans une PME près de Nantes…
Notre client : Entreprise de 30 personnes produisant et commercialisant du mobilier de bureau haut de gamme. Tient à se démarquer par une qualité irréprochable et un délai de livraison garanti.
Problématique : Retards chroniques de livraison malgré l’énergie dépensée à suivre le planning.
Diagnostic : Les commandes spéciales perturbent le flux des produits standards. La pagaille générale empêche la prise de décisions rapides et adaptées.
Décisions
- Créer un îlot ‘’Commandes spéciales’’ très simple à piloter et rationaliser le flux des produits standards.
- Ordonnancer la production par couleur de panneau mélaminé.
Actions
- Réimplantation des machines selon la cartographie définie et affectation d’un compagnon très expérimenté sur l’îlot ‘’Commandes spéciales’’.
- Affichage et suivi du planning hebdomadaire par couleur de panneau mélaminé.
Résultats
- Les opérateurs sont autonomes.
- L’avancement des opérations se ‘’lit’’ dans l’atelier (ex : pièces bleues toujours en cours le mercredi = retard !!!).
…au reengineering complet, en 2 ans, d’une ETI en région lyonnaise !
Notre client : Entreprise de 200 personnes produisant et commercialisant des systèmes d’accès pour travaux en hauteur. Vient d’être acquise par un groupe industriel à une holding financière.
Problématique : Les performances industrielles ne sont pas au niveau des ambitions du groupe.
Diagnostic : L’organisation industrielle est trop taylorienne.
- Processus structuré par métier et non par typologie de produits.
- Ordonnancement centralisé dans les bureaux, les managers de proximité ne sont pas impliqués.
- Lead time beaucoup trop important pour répondre à la demande des clients.
- Aucune dynamique d’amélioration continue.
Décisions
- Découpler la fabrication des composants (découpe et emboutissage) des secteurs d’assemblage.
- Structurer les opérations d’assemblage et de finition en 3 lignes de produits.
- Déléguer le pilotage aux 4 responsables de ligne (débit + 3 lignes produits) en place
Actions
- Mise en place du stock de découplage et de son outil de pilotage, sans changer l’ERP.
- Réimplantation des machines des 4 secteurs selon les flux physiques (chantiers Hoshin).
- Nomination d’un responsable de production plus proche du terrain et création du poste de responsable logistique.
- Mise en service de nouveaux outils de pilotage (ERP existant + Excel) en logique de flux tiré.
- Mise en place d’une réunion quotidienne de pilotage avec les 4 responsables de ligne et le responsable de production. Les cas critiques sont remontés au service logistique.
- Implémentation d’une démarche d’amélioration continue appuyée sur le nouveau responsable de production.
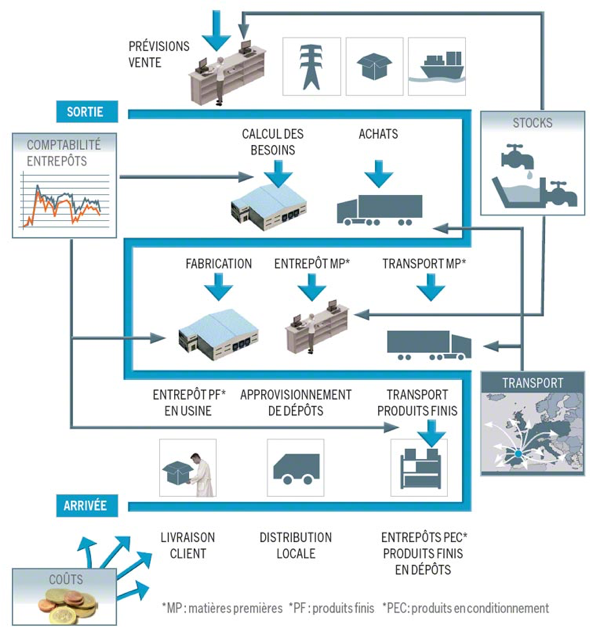
Résultats
- Les responsables de ligne sont très impliqués dans le pilotage quotidien, pour une meilleure performance.
- Lead time réduit de 50% sans augmenter les stocks.
- L’amélioration continue est structurée autour des managers de proximité.